Troubleshooting issues with a paper tube machine is an essential skill for manufacturers aiming to maintain optimal production quality. In this guide, we'll explore common challenges faced during paper tube manufacturing and delve into effective solutions to ensure the seamless operation of these machines.
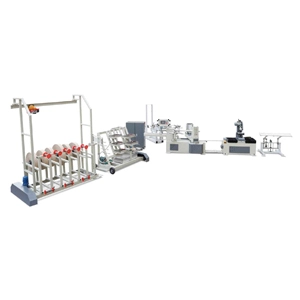
Addressing Uneven Spiral Lines on Paper Tubes
When encountering irregularities in the spiral lines of paper tubes, it's crucial to consider three key aspects:
Friction Resistance from Laser Cutting Heads: One possible cause may be excessive friction resistance caused by the laser cutting heads of the paper tube equipment. Investigate and adjust the cutting parameters to reduce friction, ensuring smoother tube formation.
Uneven Application of Lubricating Fluid: Uneven lubrication on the outer layers of the paper tube can result from irregular application of lubricating fluid. Check the lubrication system, ensuring even distribution across all layers to promote uniformity.
Insufficient Belt Support: Inadequate support from the paper bag tube forming machine's belts can contribute to uneven spiral lines. Evaluate the belt tension and support mechanism, adjusting as necessary to provide optimal support during the manufacturing process.
By addressing these points, manufacturers can identify the root causes of uneven spiral lines and implement solutions for a more uniform and high-quality end product.
Resolving Surface Imperfections on Produced Paper Tubes
Frequently, issues arise when the surface of produced paper tube products lacks uniformity. This problem may be attributed to disparities in the perspective of the two belts in the tube winding machine, resulting in uneven pressure on the paper tube. In such cases, a practical solution involves adjusting the handles appropriately based on the specific operational conditions.
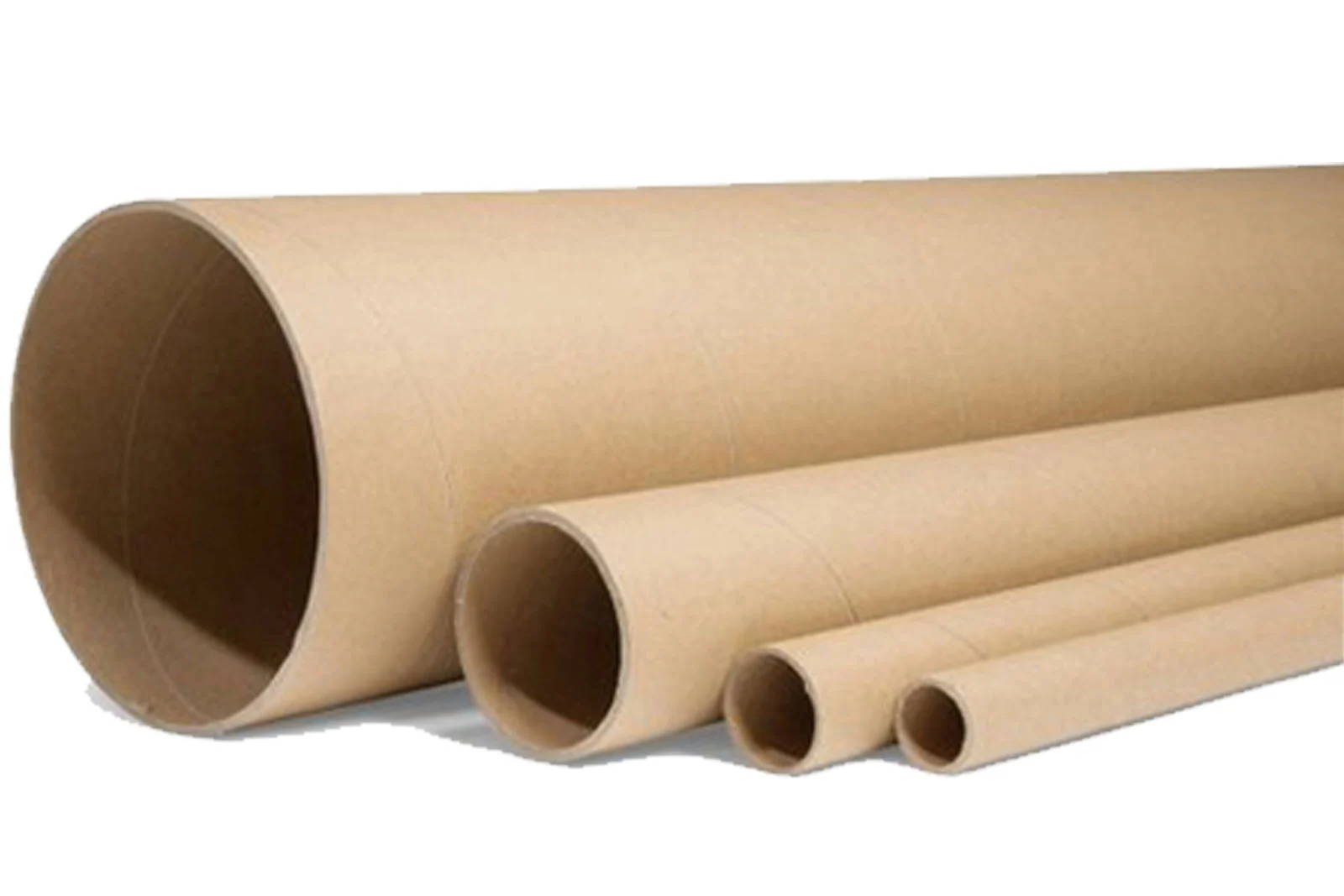
Ensuring Uniform Distribution of Adhesive on Paper Tubes
Uneven distribution of adhesive on paper tubes is a common challenge with potential dual causes:
Inadequate Angling of the Cutting Blade and Paper Strip: Insufficient angling of the cutting blade and paper strip can lead to uneven adhesive application. Adjust the angles to promote a more uniform spread of adhesive during the manufacturing process.
Unclean Cutting Blades: Residue on the cutting blades can hinder proper adhesive distribution. Regularly clean the cutting blades to prevent contamination and ensure consistent adhesive coverage.
Optimizing Adhesive Quantity
Whether it's too much or too little, improper adhesive quantity poses risks. Manufacturers should assess their specific circumstances and adjust the cutting blade angles accordingly. This proactive measure ensures the paper tube machine maintains normal operation and prevents complications associated with excessive or insufficient adhesive.
Troubleshooting a paper tube machine requires a comprehensive understanding of potential issues and effective solutions. By addressing uneven spiral lines, surface imperfections, adhesive distribution, and optimizing adhesive quantity, paper core machine manufacturer can ensure their paper tube machines operate smoothly, delivering high-quality products consistently.